28 - Engine woes
- andycbryant
- Feb 4, 2018
- 4 min read
An ignition system was rigged up and the engine primed with oil. The timing was set to the workshop manual. It took a few attempts but the engine fired into life for the first time in decades. The engine was running without coolant so the run was short. It was then left to cool for 24 hours before the head was re torqued & the cooling system filled with waterless coolant. It was then a case of undertaking engine test runs to verify everything was working. This also included engaging the gears to observe the drive train working.

As the engine runs progressed it was observed that vapour was being produced from the oil filler. Observing the coolant produced no immediate signs of head gasket issues.

However, it was not too long before the coolant began to show signs of oil contamination.

And then slight bubbling could be seen between the head and block. The head gasket was almost certainly at fault, so the only choice was to stop the tests and take the head off to see what was going on.

An inspection of the oil also confirmed fluids were swapping places somewhere.

Clear evidence of coolant entering the cylinders as well as mis firing.

Cleaned down and ready for a new head gasket. This time it will be more similar to the original pattern.

The skimmed head was also pressure tested and passed. A couple of the valves were also re seated so compression should be up. The process of fitting, torqueing and test firing begins again.



However, it quickly became clear that oil was still finding its way into the coolant. Evidence of mis firing was also still present as well as scoring on the inside of the cylinder.

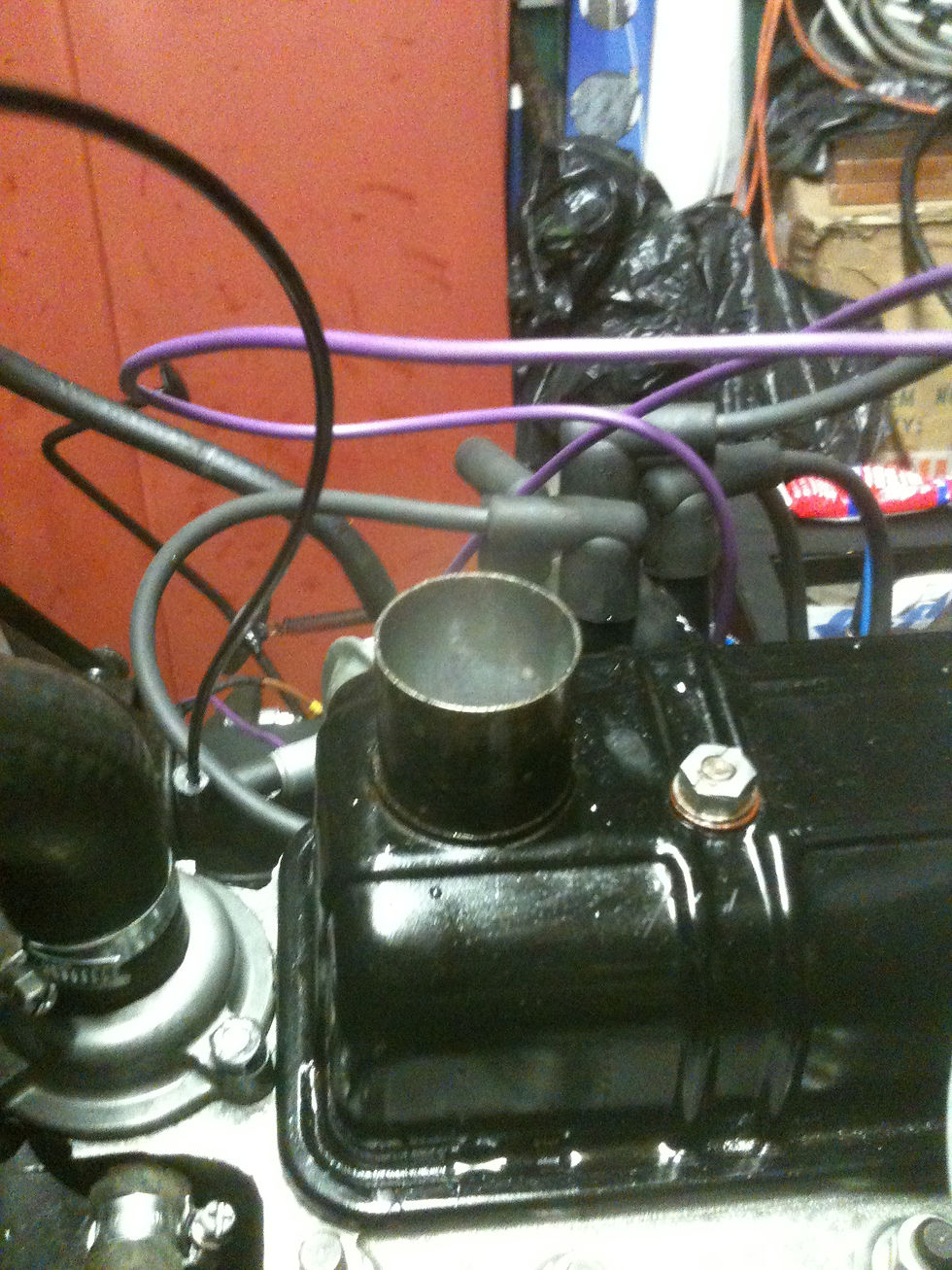


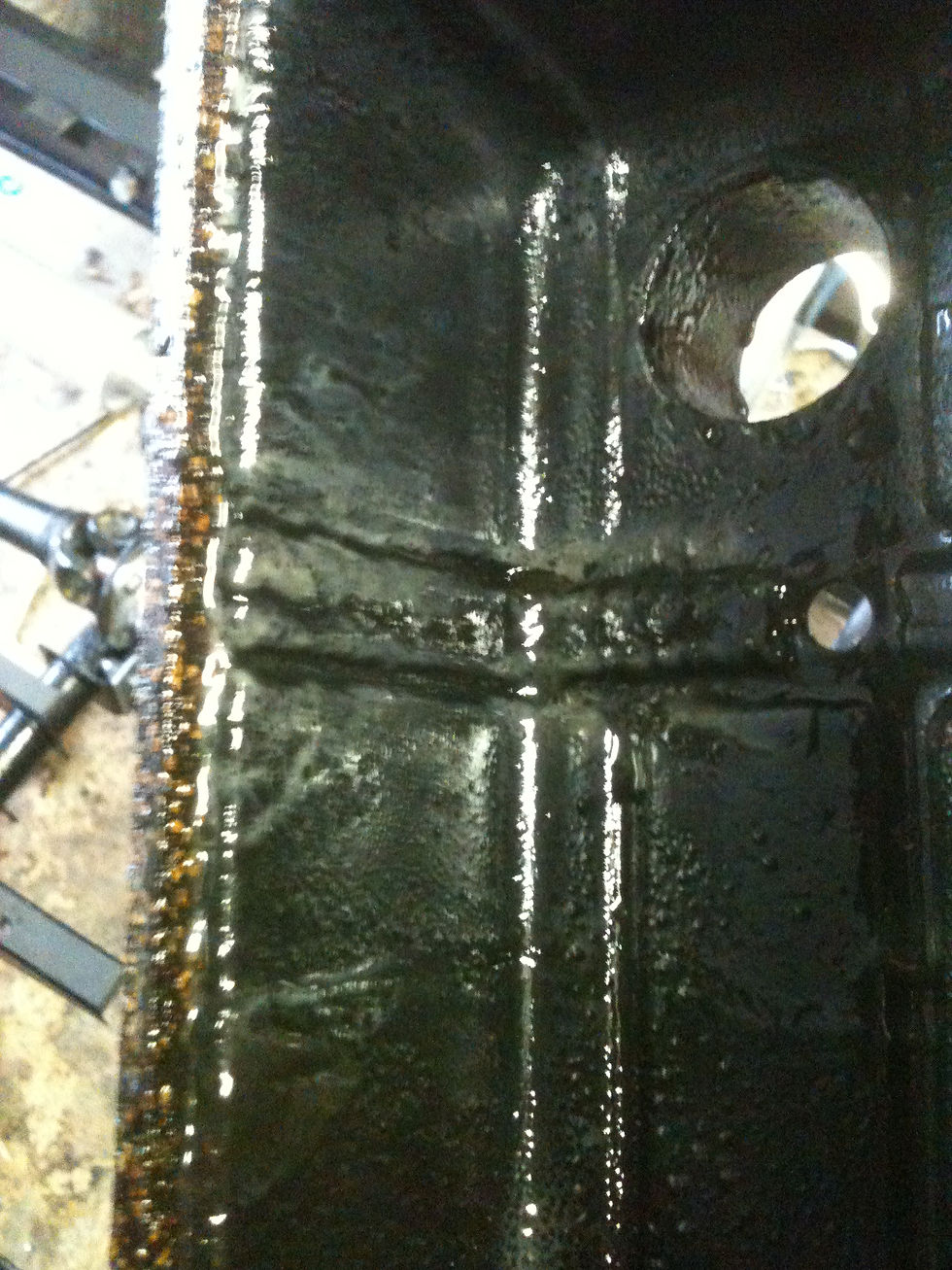
Another test and another failure. the engine was running roughly and still steaming.


The coolant was completely emulsified with engine oil. There was something very wrong & so with a heavy heart it was decided to carry out a full strip down of the block including removing the liners to inspect the condition of the oil galleries behind cylinder 4. At the same time I decided to commission a spare engine I had purchased. Listed as a factory recon engine it was a late style 600cc block. It therefore required some additional parts.
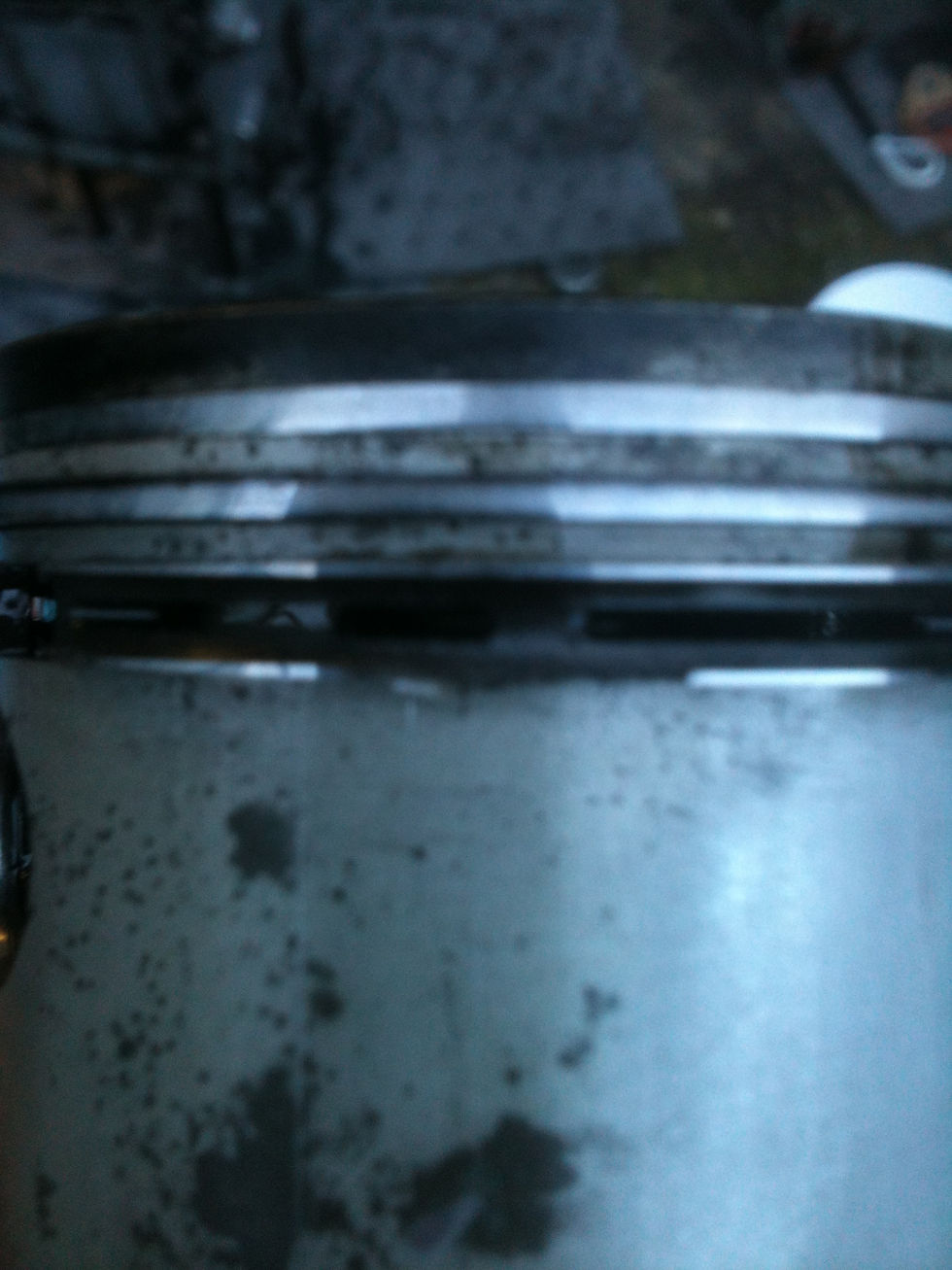

Stripping the block also revealed damaged piston rings. That explains the scored surface of the cylinders!
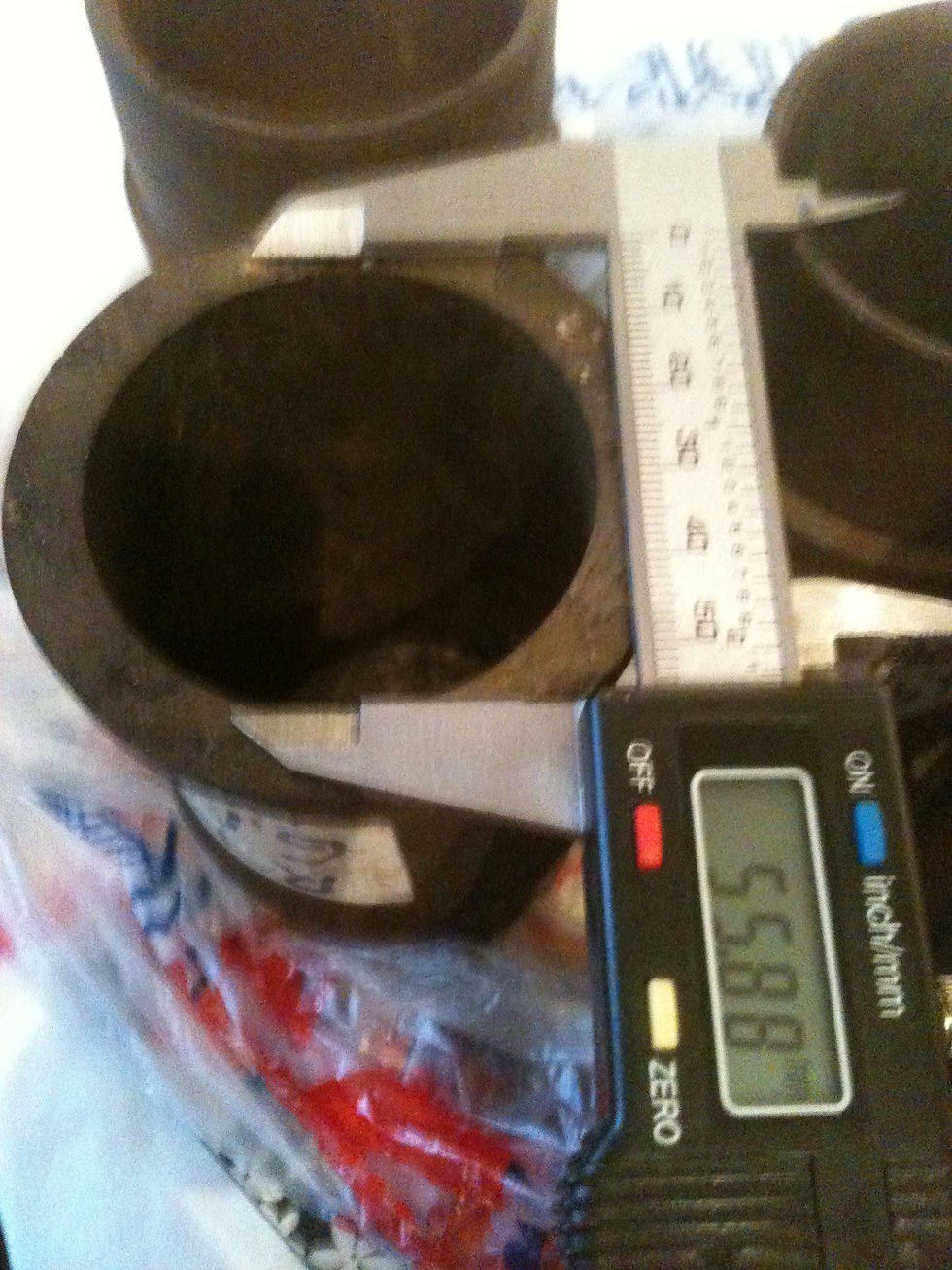
I was very lucky to have a set of NOS wet liners.

It was during the strip down that the fuel pump pipe connection came apart. Had this happened on the road it would have squirted fuel straight up onto the distributor. I will revert to the later AC type J fuel pump set up.


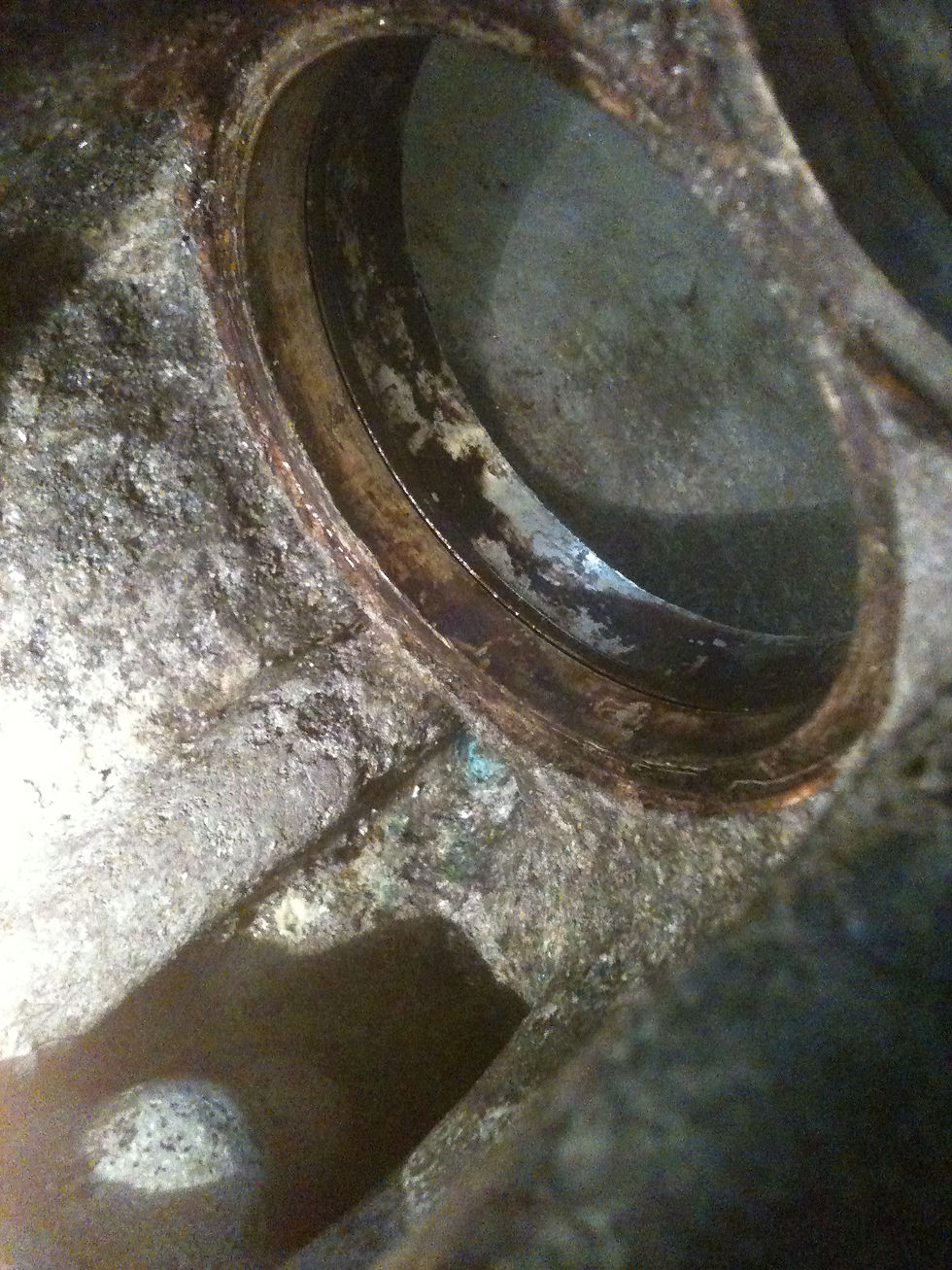
The wet liners would not press out. The block had to go to a workshop in order to have them removed. Even then one shattered. With the liners out the extent of alloy erosion becomes clear. Oil contaminated scale deposits indicate the gallery is compromised so an engineering solution is required. The plan is to drill out the vertical gallery to just past the erosion. An alloy sleeve will then be fitted to seal the leak and return the gallery to the required diameter.

A local engineer produced the sleeve and it is ready to be pressed home.

And now ready for re assembly.


Two different styles of wet liner. It turned out I had an odd one, which probably fitted the later 600cc block so there was a wait whilst the odd one I needed was tracked down.

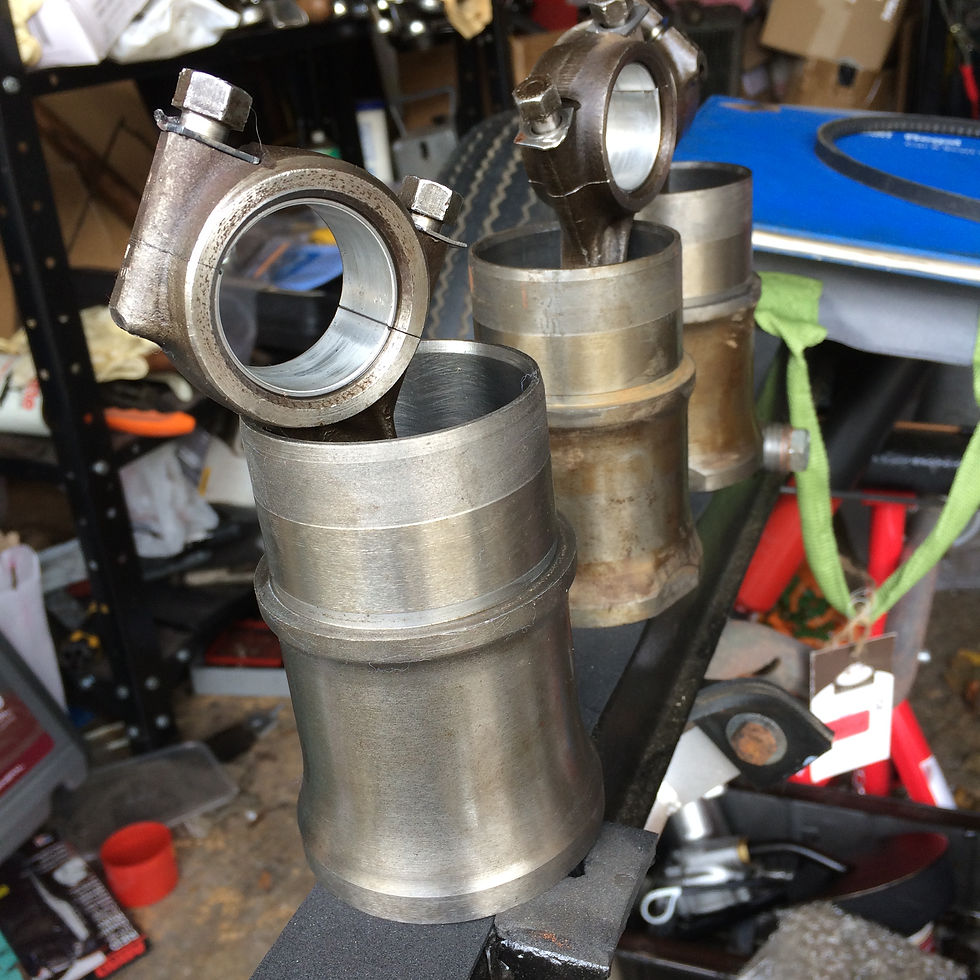
New liners with the pistons ready to go to the engineering shop.
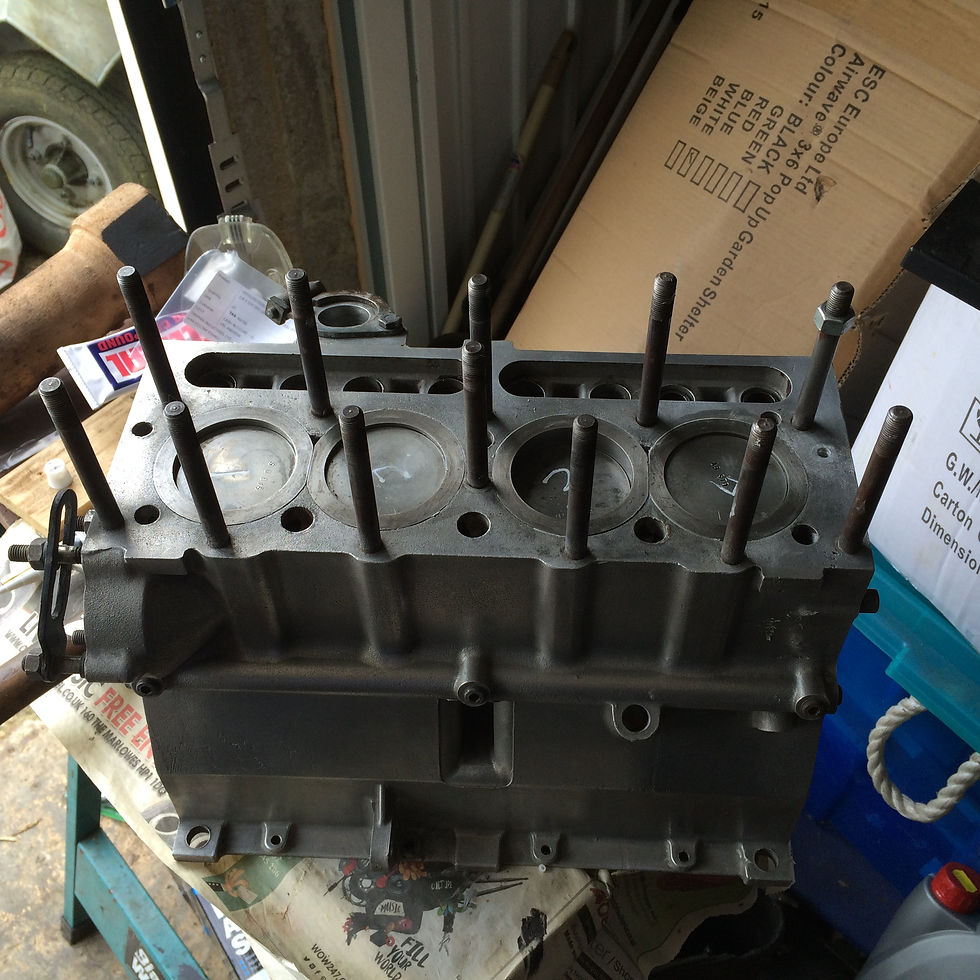
The block returns with the bores honed, the piston rings checked for burrs and the correct gap. Using an old gasket the head was torqued down to ensure the liners seated correctly whilst the sealant set.
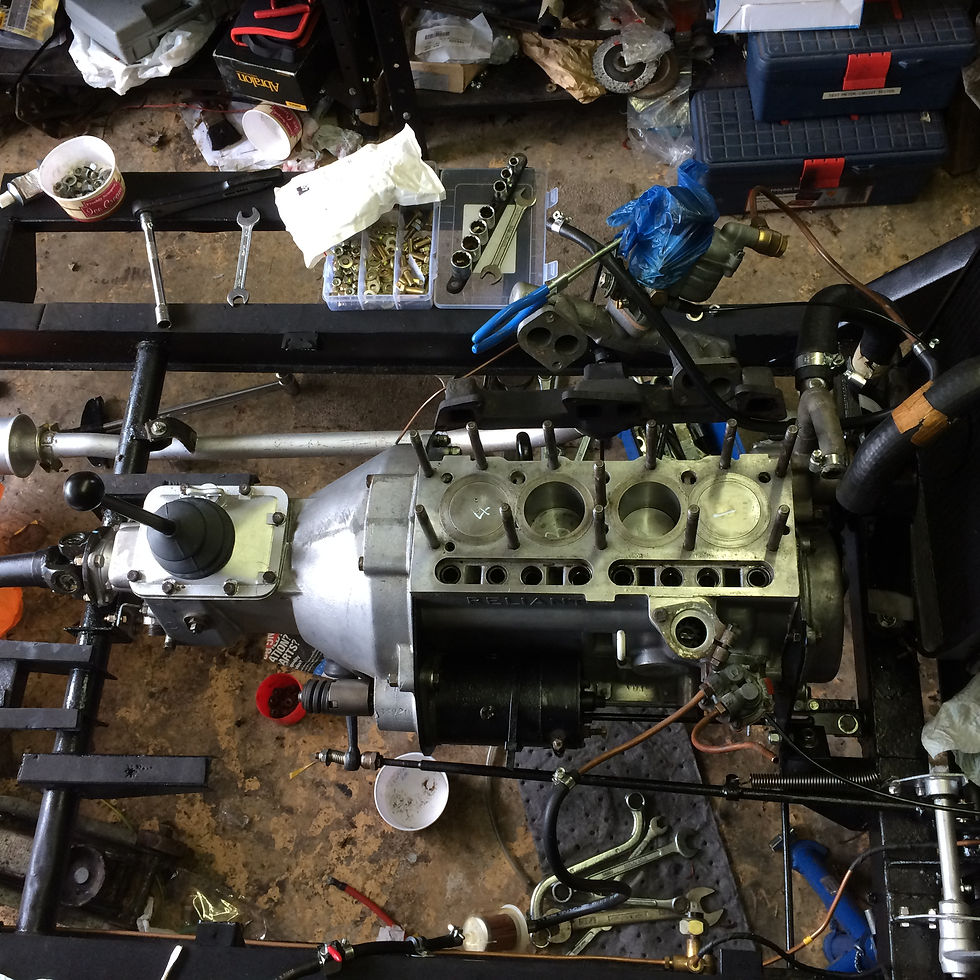
And back it all goes.

Ready for testing once again. Except during the rebuild the oil pump spindle was not orientated correctly putting the timing 180 degrees out.


Getting the distributor seated properly also stopped oil spraying out !
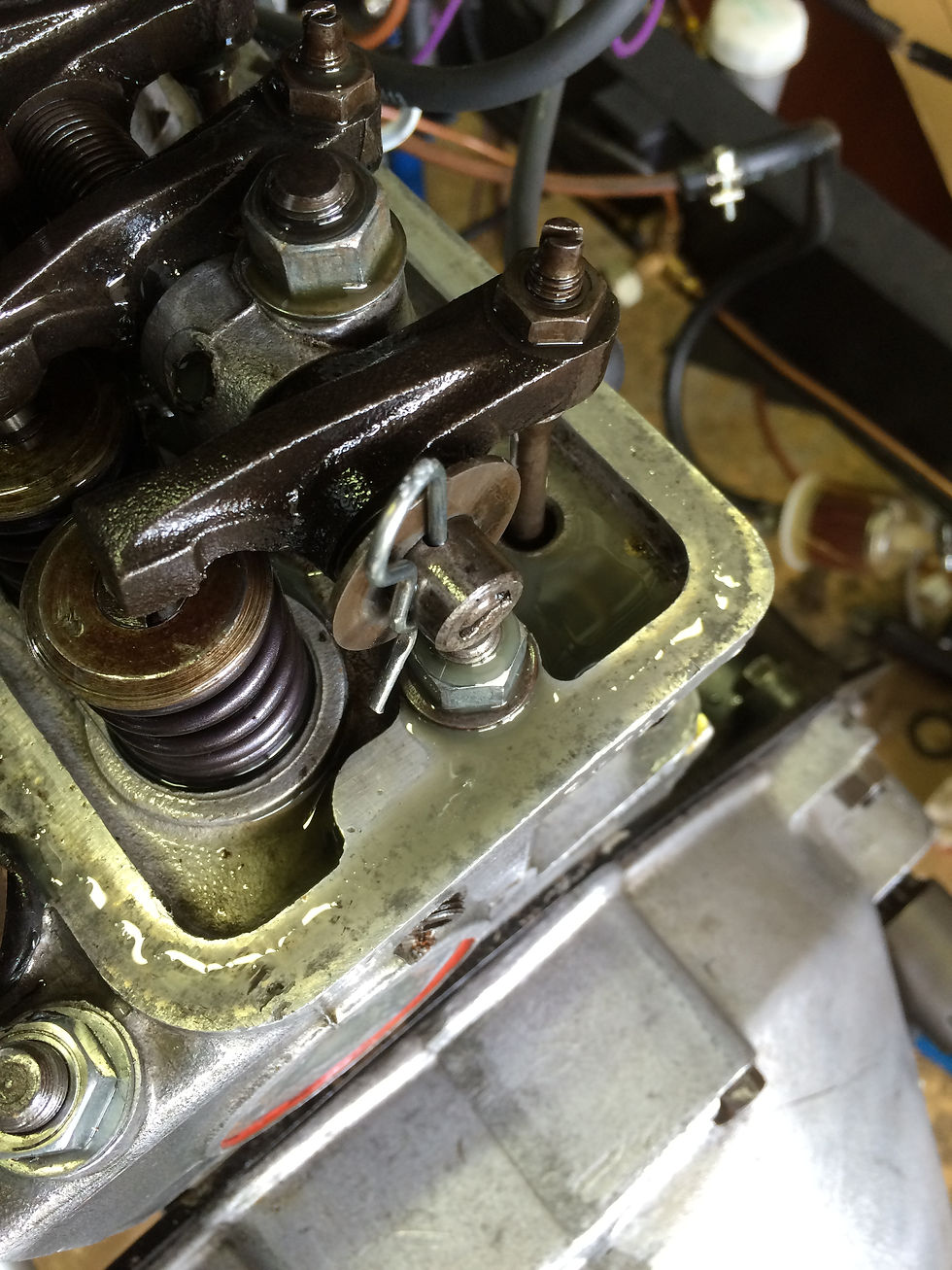



May 2016 and after months of work the engine is still putting oil in the coolant. Not only that but I managed to put the oil pump spindle in out of alignment so timing is 180 degrees out ! A belated check of the level across the cylinder block revealed a dome around the central stud. This is not that uncommon but by skimming the head, I effectively made the seal worse. Once again it was decided to strip the block and take it to be levelled off. With the liners back out I also investigated various industrial alloy resin repair products to bolster the eroded alloy. I found a suitable product that can be mixed to a pourable consistency in order to get into all the cavities.

Extra attention will be paid to ensuring enough high temperature silicon sealer is used around the seat of the liner.

This should also prevent coolant seeping through the rear of the block.
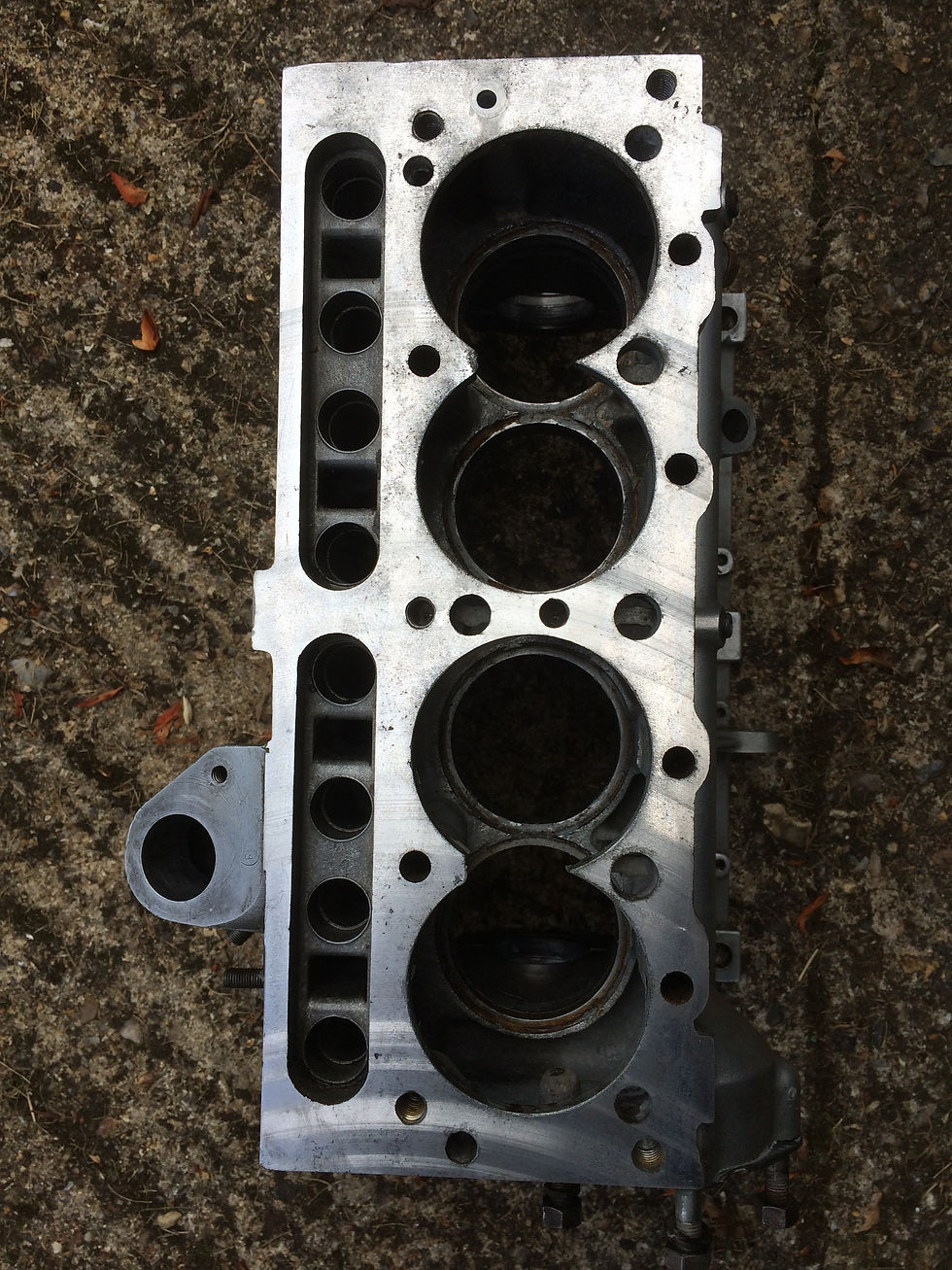
The skimmed block is now flat, so the cylinder head should make a good seal at last. Now to put it all back together.
Comentários